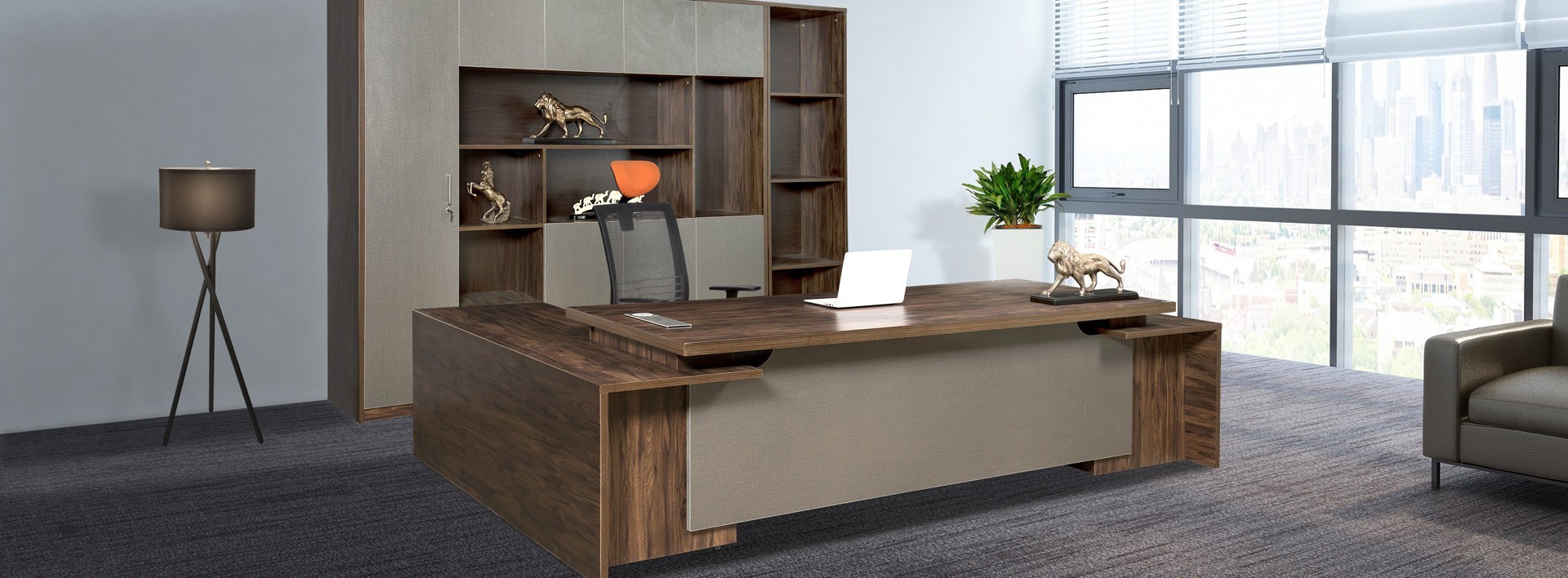
Identification sign
Currently, on the market, there are a number of counterfeit/fake products with designs and patterns similar to those of The One Furniture Joint Stock Company. Therefore, to protect the interests of consumers, the company introduces guides for customers to identify genuine The One Furniture products as follows:
Visual cues:
1. Guarantee Stamp
Anti-counterfeiting stamps are mounted on all product lines of The One Furniture, including: office furniture, home furniture, school furniture, furniture for public works and hospitals. The One Furniture's anti-counterfeiting stamp has a size of 25mm x 40mm, usually attached on the main components and individual positions of each product to practice anti-counterfeiting.
In many cases where it is necessary to compare and verify, the manufacturer can determine whether the product is genuine or fake. The stamps have a printed logo according to the new identity, a character code and a 7-digit series of jumping numbers according to the manufacturer's own regulations, helping to distinguish the origin (manufacturer) and time of manufactering. In particular, the stamp has a separate QR code for each product line to help customers easily trace the origin of the product through the website www.noithattheone.vn.
(Image)
When customers shine an ultraviolet (UV) light on the stamp, the Logo cluster will glow red, and the character code "TO xx" will glow with a prominent blue light. At the same time, customers can use applications with integrated QR code scanning feature such as Zalo, Viber, Icheck, Facebook... to access the website and verify the product's origin. The application will automatically access the category corresponding to each product at the official website of The One Furniture (www.noithattheone.vn).
(Image)
2. Product Label
1. Warranty service
The One Furniture JSC processes product warrenty through our 1st-tier authorised dealers. Thus under error-occuring circumstances, Customers please take the following steps:
- Step 1: Provide product status, product stamp number and warrenty requirements to the authorised dealer the Customer made their purchase (delivery note). The authorised dealer is responsible for informing us.
- Step 2: The One will analyse and verify provided information. After the analysis process, we will inform the Customer of warrenty solutions and warrenty time.
- Step 3: The One and the Customer agree on one warrenty solution as well as a suitable date.
- Step 4: Implement the agreed warrenty solution. This will be carried out by the authorised dealer with whom the Customer made their purchase.
2. Warranty period
- For Safe codes KA, KT, KKS: Warrenty periods are 24 months and 12 months for body and accompanying accessories (locks, handles,..) respectively.
- For Fireproof Safe codes KS, LG, PI: Warrenty periods are 36 months and 12 months for body and accompanying accessories (locks, handles,..) respectively.
- For imported safe codes PS01, PS02: Warrenty period is 6 months.
- For other safe products: Warrenty period is 12 months.
3. Warranty conditions
- The product is damaged, faulty due to manufacturer's fault.
- The product is within warranty period.
4. Conditions not covered by warranty
- The product is out of warranty period.
- Damage is not caused by the manufacturer, but by the user not following the manufacturer's instructions for installation, use, and maintenance. Improper use and failure to follow the manufacturer's recommendations.
- Damage caused by the buyer's transportation.
- Damage caused by force majeure such as storm, flood, fire, earthquake.
- Damage caused by wood expansion due to misusage and/or improper maintenance e.g exposure to water or high-humidity environment.
- Damage caused during product display.
5. Warranty cost
- Free warranty for all damaged products due to manufacturer's fault.
- For products that are not damaged due to the fault of the manufacturer, the company will charge a warranty fee, the warranty cost will be agreed between the company and the customer.
6. Regulations on products required for inspection upon despatch/delivery
Upon product receipt, please inspect according to the following product list:
No |
Product Code |
Analyse and Inform Service and Warrenty Department |
Procedure |
1 | Assembled painted wood cabinet: TP01, TP02, TP3, TP04,TP06H1, TP06H2, TPV1, TPV2, TPV3 |
- Inspect immediately upon despatch/delivery (Open box and check if any errors occurred)
- For stone surface: check for cracks on the back surface and for signs of colliding outside the box on the front surface - Inform service and warrenty department and return unqualified product. |
- Stocker requests driver to inspect and confirm on delivery note.
- In case a product on the regulated “Poducts required for inspection” list is found unqualified while inspecting before despatching, Customer / authorised dealer holds the right to request driver to confirm and inform the service and warrenty department to process. |
2 | - Glasses on wooden storages: HP, SV, NT, HR, AT, LUX - Steel and painted storages - Glasses on sofa tables, high-class dining tables, coffee tables, natural-wood tables - Stone surfaces |
||
3 | - All products in High-glossy and stone-surface lines (if any) | ||
4 | - TQ18 – 26 Seatings - Office and Home Sofas |
||
5 | Bar Stools: SB30, SB31, SB32, SB33 | ||
6 | - TQ, GH Seatings - Safe - Other products |
Check for recognizing signs intact on accompanying accessories, manufacturing packaging. Inform Service and Warrenty Department and return the product if unqualifed. Please report any issues within 24 hours upon receiving the product. |
I. General instructions
1. Do not scratch the surface of the product with sharp objects.
2. Do not use cleaning chemicals on the surface of all products.
3. All products are stored in a dry place, avoiding termites, avoiding direct sunlight (all The One products are appropriate for indoor usages).
4. Racking system, pallets need to have the same size as the product packaging size, avoid placing products with large packaging sizes on pallets and shelves with a much smaller size which will cause flattening, broken, broken product. The pallet structure is sturdy ensuring not to be broken or tilted to avoid damaging the product. Suitable pallet size is 1950 x 1200 mm. Pallet height >150 mm.
5. The packaging has no holes due to the posibility to have loss of details and accessories during transportation. For products whose packaging is torn during storage, it should be re-covered to avoid loss of details and accessories inside the packages.
6. Products should be neatly arranged, not tilted to avoid the risk of falling when storing, loading and unloading.
7. When loading the products, pay attention to the principle of heavy goods below, light goods above, products with sharp and pointed ends should be arranged in separate areas to avoid causing damage to other products.
8. When loading on the trucks, absolutely do not stack sofas next to sharp objects without protective padding, priority to place them separately. In some cases, the bottom of the truck has semi-finished products or other hard and sharp materials, before loading the products, a layer of salvaged wood/cartoon cover must be spread to create a flat and safe surface for the products stacked on top.
9. For products with glass: The glass should be kept separate and have identification signs. With separate boxes, the glass should be arranged vertically. For products with built-in glass, be absolutely careful not to step on, toss, or stack heavy objects on top of the product.
10. Comply with the symbols on the package: avoid moisture, fragile, correct direction, do not step on the product, avoid sunlight...
11. For products with disassembled structure after using from 6 to 9 months, it is necessary to check and re-tighten bolts and screws once.
12. Perform first-in, first-out, last-in-last-out to avoid long-term inventory, affecting product quality, causing deviations when installing products before and after improvements or out-of-fashion…
II. For home products
1. During transportation
- When carrying, it is necessary to keep the product vertical to avoid breakage.
- Sofa tables, TV shelves, dining tables need 2 people to carry when transporting. Do not toss the products.
- When stacking on a truck or lifting, four sofa legs should touch the floor gently.
2. During preservation and storage
- Various types of stone and glass surfaces are arranged along the length without overlapping or lying down.
- Do not stack more than 2 products of Sofa tables, TV shelves, dining tables... on the same pallet, the main side should face each other.
- All kinds of dining chairs are stacked in 2 pieces, the seats face each other.
- Sofas are arranged upright or lying down according to the position of use, not stacked on top of each other. Particularly sofa01, 02, 03, 306, 308, 311, 313 must lie down. Avoid placing next to sharp objects.
3. During usage:
- With sofas:
+ Do not trample on the chair, do not leave sharp objects such as pens, knives, scissors ... on the surface of the product. Do not place in a place where there is direct sunlight, do not place near indoor bonsai pots because it is easy to shoot when watering.
+ Periodically 1 -2 months / time cleaning with a slightly damp rag. Do not use chemicals to clean as this will cause skin explosion or color fading.
- With different types of dining tables and chairs:
+ Do not place heavy objects on the table or collide with the table. Do not contact hot objects with the tabletop, do not place near heat sources…
+ Clean the surface of the product regularly when it is contaminated with grease, food, etc. with a dilute dishwashing liquid. Then wipe again with a clean damp rag and dry the surface of the product.
- With TV shelves, sofa tables, tea tables:
+ Do not sit, step on the product, do not expose the product to direct sunlight
+ Periodically 1-2 months cleaning with a slightly damp rag. Do not use chemicals to clean as this will cause skin explosion or color fading.
- With bedroom furnitures: beds, wardrobes, chalkboards, taps.
+ Clean regularly, keep the room dry and ventilated.
III. For products made from steel tube, inox
1. During transportation:
- Must be gingerly, do not toss, dragging will dent the edge, scratch the surface of the product, leading to the product rusting quickly.
2. During storage:
- Products must be neatly arranged, neatly aligned, must not be tilted, slanted, deviated to minimize the risk of breakage and product damage.
- Products with different properties must be placed in different areas. Do not load heavy goods next to fragile goods such as glass, plastic, etc.
- The maximum height when arranging a stack of products is 1.8 m to facilitate loading-unloading and transportation.
- For BHS, BSV product lines: Stacking 7 boxes with BSV products and 8 boxes with BHS products. Do not place the product in a prone position, which may cause distortion and breakage of the box.
- For MC hall chairs, no more than 7 seats per 1 stack must be arranged and the products must have dust- and scratch-resistant nylon.
- Products that are only packed in plastic packaging (G chair, PC beam, MC chair, bed ...): products should be arranged neatly, avoiding contact with sharp, rough details to prevent damage to the packaging.
3. During use:
- In case of using the product in a wet or flooded environment, wipe the product with a dry soft cloth.
- Regularly clean the product with a soft dry cloth. This will keep the product always shiny and not rusty.
- When not in use, the surface of the product should be cleaned, it is best to wipe a layer of anti-rust oil on the surface and the product must be stored in a dry place.
- For chair products, the users should sit with the right posture, the right center of gravity, do not climb, step on the seat cushion, do not sit down with a free posture, it will create a sudden force that is easy to damage and deform the product. To ensure quality and durability in use, the net weight acting on the seat cushion should be less than 100 kg.
- For stainless steel dining table products, the table surface should be cleaned to avoid food stains, grease affecting product quality.
- Composite surface products should be placed in a cool place to avoid high temperatures, use the correct type of standard feet to avoid warping.
- Plastic products should be used in a covered environment to ensure quality and durability during use. Avoid the direct exposure to the sun, which affects the quality, mechanical properties and color of the plastic mattress.
IV. For industrial wood products, painted wood products
1. During loading and unloading, transportations:
- Large and heavy boxes (>40kg) and prepackaged products need 2 people to carry. No rhyme or free drop the products from the truck.
- The product boxes having pre-installed glass should be unloaded gingerly.
- When unloading, do not prop one end of the package to the ground.
2. During storage:
* Products of PU and Veneer painted desks and cabinets:
- The product packages should be arranged in the direction with the largest contact area with the pallet.
- Do not arrange more than 10 boxes/stack, one stack is not more than 1.4m high. For auxiliary cabinets, do not arrange more than 2 boxes/stack, for drawers, do not arrange more than 3 drawers/stack.
* Melamine industrial wood products:
- The product packages should be arranged in the direction with the largest contact area with the pallet.
- Workbench products cannot be arranged more than 1.8m/stack.
- Drawers can be arranged up to 3 boxes/stack
- The length of the cabinets: Do not arrange more than 1.5m/stack
3. During use:
- Do not hold the table top and drag the table legs when moving the products (desks, meeting tables...) but need to lift the table legs to move.
- Do not place sharp objects, too heavy objects on the surface of the product, keep the products away from water and heat sources. Do not sit on the table.
- In case the product gets wet, it must be wiped dry with a soft dry cloth immediately to prevent water from getting inside.
- Product cleaning: The surface of the product needs to be regularly wiped with a clean, soft cloth.
- In particular, the details on metal products need to be cleaned with a soft cloth, avoid using water to wipe because it may oxidize leading to rust.
V. For office chairs and sofas
1. During loading and unloading, transportations:
- Do not pull, drag or push the product on the floor, which can easily scratch the packaging, cause mold, and damage the product inside.
- When moving the sofa, it must be lifted gingerly, do not slide on the floor, which is easy to break, break the foot sole, when lifting, you must cling to the part with the wooden frame to avoid tearing the seams on the product.
2. During preservation and storage:
- Staff line of chairs: Stacked on pallets for no more than 3 turns, the bottom box is always stacked vertically.
+ Series SG550, SG555... stacking up to 1.8 m in height (maximum 36 boxes/pallet).
- High-class leather chair line: Stacked on pallets for no more than 2 turns, the bottom box is always stacked vertically.
+ Series SG1020, SG350, SG913 ... stacking up to 1.8 m in height (maximum 24 boxes/pallet).
- With cushion packaging: Stacking on pallets for no more than 3 turns, stacking up to a maximum height of 2 m, do not stack products in the direction of the used surface on the floor or pallet.
- Middle back, high back chair line: Stacking on pallets no more than 3 turns in vertical direction, stacking maximum height of 2.2 m - 12 boxes/pallet.
- China high-class leather chair line: do not stack the product with direction of used surface contacting the floor or pallet, do not stack it sideways, do not stack the second product with the base of the leg in contact with the used surface of the first product. When stacking the next one, turn the second one upside down (the 2nd cushion is placed on the 1st headrest and the 2nd headrest is on the 1st cushion). Do not stack more than 2 products.
3. During use:
- Industrial DP, PVC leather and real leather products must be stored in a cool, dry environment, avoiding exposure to heat sources and direct sunlight for a long time. When cleaning the product, do not use detergent to clean it, just use a dry cloth.
- Do not sit on the arm of the chair to avoid breaking or tipping the chair.
- Do not sit in a chair with a free-standing position to create sudden force, which can easily damage and deform the product, especially with the kneeling SL meeting chair line.
- Staff swivel chairs, staff mesh chairs, child chairs must have the correct posture. Should not sit with both feet on the chair and lean back to push the chair back, which can easily cause deformation, tilting the seat back.
- Do not twist the elastic mechanism on the seat too loosely to prevent the seat back from falling.
- Do not leave sharp and pointed objects on the surface of the chair to avoid scratching or tearing the surface covered with leather upholstery, industrial leather, felt fabric.
- For SG 527, SG 528 products, it is recommended to tighten the back lever lock knob before use and pay attention not to install the backrest too low to touch the seat cushion.
- Periodically every 6-9 months check and tighten screws at the armrest position, chair backrest cushion to ensure the chair structure is limited loosely that can cause noise when in use.
VI. For strongboxes and safes
1. Strongboxes
* During loading and unloading, transportation:
- Do not rhyme or drop freely from the truck.
- The packages having pre-installed glass should be unloaded gingerly.
- When unloading, do not prop one end of the package to the ground because it will cause flattening of the head.
* During preservation and storage
- Product boxes should be arranged in the direction with the largest contact area with the pallet (except for pre-assembled goods, eg: HS1, TU118-7D).
- For the long parts of the cabinet: Do arrange no more than 10 boxes/stack to avoid flattening the products below as well as to facilitate loading and unloading and limit the possibility of tilting, falling.
- For short products: Products need to be placed horizontally, not vertically. Do not arrange more than 12 boxes/stack.
- For iron drawers with wheels: only arrange 2 items/stack, two roofs facing each other.
- For crates: do not arrange more than 3 products, stack vertically (as the direction in use).
* Instructions for using strongboxes - bookshelves
- Assemble the product in the correct order and specification as on the assembly instruction paper.
- The load should be evenly distributed on the surface of the product during use.
- Using the correct type of assembly tool, install a sufficient number of accessories into the product according to the assembly instructions.
- If the floor is not flat after assembling, the cabinet door gap will be uneven, the ground need to be re-positioned before use the cabinet.
- Do not disassemble the cabinet R when transporting or changing position during use.
- MCF products should be checked and lubricateds, couplings, etc... every 3-6 month to avoid making noise. Re-tighten the bolts and nuts to avoid loosening and distorting the structure.
* Use the correct load capacity of the product as shown in the table below
No | Product | Weight |
1 | GS3 | Do not load more than 30 kg/batch |
2 | GS1A | Do not load more than 30 kg/batch |
3 | GS1B | Do not load more than 30 kg/batch |
4 | GS2K1 | Do not load more than 30 kg/batch |
5 | GS2k2 | Do not load more than 30 kg/batch |
6 | GS5K1, GS5K1B | Do not load more than 40 kg/batch |
7 | GS5K2, GS5K2B | Do not load more than 40 kg/batch |
8 | GS5K3, GS5K3B | Do not load more than 40 kg/batch |
9 | GS5K4, GS5K4B | Do not load more than 40 kg/batch |
10 | GS5K5, GS5k5B | Do not load more than 40 kg/batch |
11 | GS6 | Do not load more than 30 kg/batch |
12 | MCF1,2 | Do not load more than 30 kg/batch |
13 | TU2F, TU3F, TU4F | Do not load more than 25 kg/batch |
14 | TU4FN | Do not load more than 25 kg/batch |
15 | File cabinet line | Do not load more than 30 kg/batch |
16 | Cabinet R line | Do not load more than 20kg/batch |
* Note: In case you use the overload according to the prescribed standards, the Company will not warranty the above product. Any arising will be resolved according to the Complaints Resolution Process.
2. Safes
* During loading and unloading, transportation:
When loading or unloading the vehicle, it is necessary to use a forklift or a person to carry it. Do not forcefully lower or throw the product making the products scratch or distort.
* During preservation and storage:
- KT, KA safes should not be stacked on top of each other because it is easy to cause flattening / settlement with cracks in the roof. A maximum of only one row can be added and the roofs are stacked face-to-face with KA22, KA40, KT36 types.
- Safes that are stacked on top of each other need a pad to avoid scratching or denting the product underneath.
- Safets should not be placed horizontally, buckle face up or down.
- For safes of under to 50kg: Do not stack more than 4 items.
- For safes of 50 to 110kg: Do not stack more than 3 items.
- For safes over 110kg: Should not be stacked on top of each other, smaller safes should be placed on top, but arranged no more than 3 items.
* During use:
- Do not arbitrarily disassemble or change the product structure when using.
- Do not change the private code of the KA safe during use.
- For electronic safes, avoid strong impact on the electronic lock and avoid contact with water. Batteries used every 03-06 months must be replaced once, use 1.5V Alkaline batteries.
- Do not use solvents, acidic chemicals to clean the lock surface, body, and door of the safe.
- Carefully read the instructions for changing the code before doing, pay attention when changing the safe code, the safe door is always open during the change.
- For electronic safes with keys and extra batteries: do not leave the battery sockets and auxiliary keys in the safe during use.
- Should regularly lubricate the lock to keep the longest product life.
Thư viện video & thủ thuật
I. GENERAL RECOMMENDATION ON FURNITURE PRODUCTS
1. All products have a certain tolerance on colors compared to those on Catalogues, price list, and color table.
2. All changes made by the Manufacturer without affecting the overall shape, texture and quality of the product are not required to be notified to the customer.
II. RECOMMENDED PRODUCTS FROM STEEL TUBE, INOX
1. Do not accept production of plating products larger than the size: 650x750x1100mm due to technological incompatibility.
2. Do not accept the production of Electro static powder coated products larger than size: 2400x1200x500mm due to incompatibility in terms of technology.
3. Do not use rectangular pipes with sizes of 40×40, 40x80mm or more in plated products due to incompatibility in terms of technology will lead to products with poor gloss and rapid rusting.
4. Do not accept plating hall chair frames, waiting room chair beams, MC chairs, VT3, VT532B, G0898, G 1499, G 1699 desks' hand due to incompatibility in terms of technology. Hoa Phat only produces plated thrones, electro static powder-coated legs for G 0398, G 0498, G 0698 products.
5. For products screwed to floor, we kindly ask Customers to inspect responsiveness of the floor surface and foundation to select suitable screw types.
6. For table surfaces not on the standard sizing list described in our Price List or incorrrect leg assembly, Hoa Phat will not provide warranty.
7. Stadium chais are suitable for roofed construction sites to ensure product quality and endurance during usage, please advise end-users to examine prior to order placement.
8. Use and store in dry places, avoid direct exposure to sunlight, water, saline environment, chemicals and disinfectants.
9. Do not use steel wipes to clean plated products to avoid scratches and shortened product durability.
10. Do not use chemicals with axid hydrochloric to clean products to avoid causing damages and rusts to product surfaces.
11. Do not spray disinfectants directly on Inox and plated products to avoid corrosion and rust on product surfaces.
12. Please use soft and dry fabric absorbed with scented petrol, RP7, WD40, Autosol to clean and preserve product surfaces.
III. RECOMMENDED INDUSTRIAL WOOD PRODUCTS
1. It is not recommended to use batch details to store items that are too long to avoid sagging during use, specifically:
– 900mm longer for 18mm thick wood, 1100mm longer for 25mm thick wood.
2. It is not recommended to use sliding vane parts with too large dimensions to ensure smoothness when opening and closing, specifically:
– 400mm wider and 1000mm taller with plastic wheels.
– Over 600mm wide and 1000mm taller with metal wheels.
3. PVC coated wood should not be used with countertops, cabinet doors, drawers and wooden partitions to avoid scratching the surface.
4. Partitions higher than 2m should not be used (if any, they must be mounted close to the ceiling to secure the connection between the walls).
5. All industrial wood products of Hoa Phat Joint Stock Company have thickness tolerances from 0.5mm to 1.2mm. Wood types include Melamine, Laminate, Simen, PVC coated wood, PU coated wood.
6. For beds with Okal wood sticks (GT40, GT40B, GC6, GC7) , please follow the instructions below:
+ During humid season and humidity is above 90%, please clean the products with dry towels 2-3 times/week. Turn on AC or fan to keep the room dry and help with ventilation.
+ During installation period prior to Acceptance, please ensure ventilation and avoid rain. Clean products 1-2 times a week with dry towels and increase to 2-3 times/week during humid season. Turn on AC or fan to keep the room dry and help with ventilation.
IV. RECOMMENDED PRODUCTS STUNNING CHAIR AND OFFICE SOFA
1. PVC material should not be used for products such as: SG216, SG225, SG301, SG704 SG711, SG721, SG801, SG811, SG1425, SL216, SL225, SL301, SL711, SL721, SL811, ... because these products have models Deep seat form, using glue to bond between PVC and foam, so it can be blistered, peeled PVC layer during use.
We do not recommend the use of PVC for products such as SG925, SG608 since PVC is not compatible with product structure and features and might cause noises when in use.
2. Do not accept the production of fabric upholstery on the TQ leadership chairs, high-grade leather seats, GH seats and Office Sofas such as SF01, SF02, SF03, SF11, SF21, SF23, SF33, SF34, SF3…
3. We do not recommended the use of PVC for seating products such as TQ, SF01, SF02, SF03, since sewing with PVC will lead to products being wrinkled, easy to absorb glue on the surface of the product, affect the surface durability of the product.
If you place an order, the company will not provide warrenty for the above product.
4. K28, Z01, Z02 fabrics and PVC should not be used for TC, SL81 chairs, etc. because these materials have great elasticity, they will be wrinkled during use.
If you place an order, the company will not provide warrenty for the above product.
5. Leather, industrial leather, PVC coated products should not be used in tight working spaces that are prone to collisions with surrounding objects, causing scratches, rapid tearing of the product. High-humidity environment will cause must and damages to the product.
V. RECOMMENDED PU PAINTED WOOD PRODUCTS
1. Do not accept the production of instant tables with dimensions exceeding 3m.
2. It is not recommended to use batch details to store items that are too long to avoid sagging during use, specifically:
– More than 900mm long for 18mm thick wood, 1100mm longer for 25mm thick wood.
3. To ensure color uniform, Customer should purchase at the same time, in the same batch. For additional order placement, colors have a 10-15% difference range compared to products already in use.
4. When placing an additional order, Customers are advised to send color samples to our factory to avoid color differences.
5. Paint codes N1, N2, N3, N4 are available for Veneer product lines. Only paint code N6 is available for Veneer-Melamine products.
VI. RECOMMENDED FILE CABINET, SAFE
* STEEL FILE CABINET, SHELF
1. For static structural products: it is not recommended to dismantle or move the product too many times.
2. Do not place the product on an incline during use.
3. Do not stack products on top of each other during use (except for cabinets).
4. We do not accept the production of powder coated products with a height of more than 2,1m due to technological incompatibility.
5. We recommend checking and maintaining, lubricating the load chain, coupling and align and tighten the nut bolt to prevent loosening during movement once every 3-6 months.
* SAFE
1. After changing the safe, try opening it a few times with the new code before closing the door.
2. We do not recommend to choose safe codes with odd, difficult to remember or numbers too close together.
3. Check and replace battery every 3-6 months. Use Alkaline battery for all electric locks.
4. It is recommended to store 01 extra key outside for emergency use: faulty electric locks, out of battery, forgetting passcode, etc.